Elevating My Knowledge
- Ryan Kulyassa
- Nov 12, 2019
- 3 min read
For many robots, an elevation subsystem is necessary. This year, our challenge, FIRST Skystone requires us to lift “stones,” small plastic blocks, and stack them onto a “foundation,” a large flat plastic plate, in order to receive points. Starting with a morphology chart to list different mechanisms, and compare their effectiveness in regards to the application in the challenge, and their compatibility with other subsystems. We then began prototyping some of these elevation systems which we thought would work best.
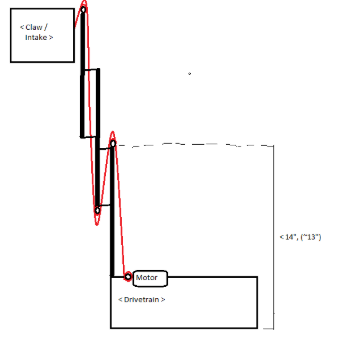
Personally, I began prototyping a two-stage linear slide elevator, with a cascading pulley system which is run throughout. The initial stages were built with REV t-extrusions and were mounted side-to-side as they were not cut to the proper length, and were not optimal for sliding. After mounting plastic REV l-brackets to the tops and bottoms of each stage, I ran individual pulleys, made out of nylon twine, throughout each stage in a cascading fashion, attaching them to l-brackets. After some trialing, the system worked, and I then began work on the construction of the actual elevator, which would be eventually mounted to the robot.

With help from a mentor, we cut brand new t-extrusions, which would circumvent the issue and assembled them to make two stages, and a base stage. I utilized the REV linear motion system to connect the stages at four unique points per stage and allow them to slide. Similar to the prototype, I attached l-brackets to the tops and bottoms of each stage. I then ran the nylon twine pulley through the l-brackets and tied the ends.
The next step in the process was motorization. As the elevator was not yet attached to the robot, and the code had not yet been fully developed for the elevator, I utilized a power supply to power the motor. We decided on using REV HD Hex motors for the robot, and the main issue I faced with this was that we didn’t have a winch that was mountable onto the hexagonal REV axle. The winch in question required two holes/pulleys, as there is one pulley which pulls the elevator up, and one which brings it back down. The only winch I could find in our current existing possession was one from Lego Mindstorms. However, the combination of these systems required a convoluted mix of Vex, Rev, and Lego Mindstorms in order to actually work. Even in the end, I faced many problems such as gears not meshing, plastic parts bending, and much more. Ultimately, the system fell to overcomplication and lack of compatibility. From this, I learned a valuable robotics lesson: combining various robotics building systems is not a good idea with the intent of performance and reliability.

I decided that the only solution to this problem was to design a custom winch, which would be compatible with the REV motor’s hexagonal axle. I designed it using CAD (computer-aided design) software, and 3-d printed it. After attaching it to the elevator, I tested the system with the motor, and the cascading pulley worked. After creating a CAD assembly of the elevator, I mounted it to the drivetrain, and the claw was mounted to the bottom of the second stage, just in time for our first scrimmage. Unfortunately, the pulley string gave out many times during the scrimmage, which was due to lack of testing with various twine strengths, etc. Due to the winch becoming covered in hot glue from constant attempts to attach the string to the winch without slipping, the system ultimately became unusable. Despite this, after the scrimmage, I re-printed an improved version of the winch, reattached the pulley, this time with stronger fishing line, and the system now works without any trouble. I also created makeshift pulleys using circular REV washers to replace the plastic l-brackets, which would be bent, and could not withstand the power of the pulley from the motor.
Looking to the future, I plan to test the system with higher voltages, applying the physics concept of voltage being equivalent to speed output. This would allow us to achieve faster lift time, which will aid in our competition performance. Also, the parts that we used can be machined, and created with materials of greater quality. Ultimately, our current elevator is a success, however, it can be greatly improved in many aspects for our future robot.

Comments